Founded in 2022, Hangzhou Shunlong Nonwovens Technology Co., Ltd. is a professional China nonwoven fabric manufacturer and non-woven raw material factory
There are many uses for non-woven fabric, and it is widely used in medical, hygiene, construction, automotive, and agricultural sectors. Unlike traditional woven and knitted fabrics, non-wovens are lightweight, flexible and affordable. They are also environmentally friendly, biodegradable, and recyclable. In addition, they are resistant to moisture and heat and provide a great deal of comfort.
Non-wovens are made by using different methods. Staple fibers can be wetlaid, airlaid, or carded and crosslapped to create a web of inter-tangled fibers. The resulting fabrics can be spun-bonded, thermobonded, or thermo-laminated. Spun-bonding is the most common method for producing nonwovens, but the choice of raw materials and bonding agents can greatly influence the finished product.
The process of creating wet nonwovens begins by submerging the raw material in water. This creates a slurry of fibrous suspension that is then treated in a mesh-forming device to create a unified, stable cloth. The most popular raw materials for wet non-wovens include polypropylene and polyester.
Polypropylene is a popular raw material because of its low production cost, high strength, and softness. The slurry is then treated with various additives to produce the desired end product. The additives can include surface modifiers, which are hydrophilic or hydrophobic. These additives migrate to the surface of the fabric and change its surface energy, which can enhance performance or lower costs.
Staple and wet non-wovens are used in a variety of applications. They are especially useful in the medical sector for surgical gowns and masks, procedure packs, underpads, and heat packs. They are also used in the hygiene industry for diapers, sanitary napkins, dust cloths, and cleansing wipes. The recent global pandemic has increased demand for these types of products. Non-wovens are also used to make fabric tote bags, which have replaced plastic shopping bags.
The manufacturing process of a spun-bonded nonwoven is more complex than that of wetland and air-laid nonwovens. Unlike wetland and air-laid nonwovens, which are made from staple fibers, spun-bonded non-wovens are made from polymer granules that have been extruded and stretched into continuous filaments before being spread evenly and laid in a web. The polymer granules are then bonded together by chemical, heat, or mechanical processes to form the final product.
The non-wovens that are produced from a spun-bonded raw material are typically thinner than those made from wetland or air-laid non-wovens. The thickness of the resulting fabric can be controlled by the selection of the raw material and the addition of fillers and softeners. These additives can also be utilized to add special properties such as anti-microbial and fungicidal protection. They can also be incorporated to provide a softer feel and improved color retention. The company also offers products that can be used to stabilize polymers and prevent degradation. This can help to reduce the amount of scrap that is sent back to the factory for recycling and can improve the quality of the finished product.
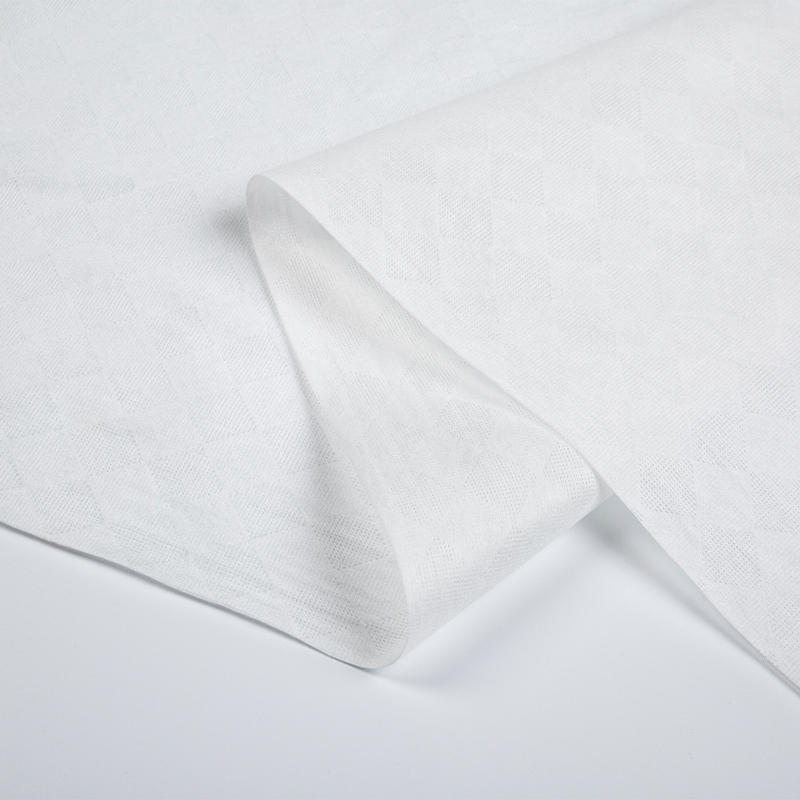
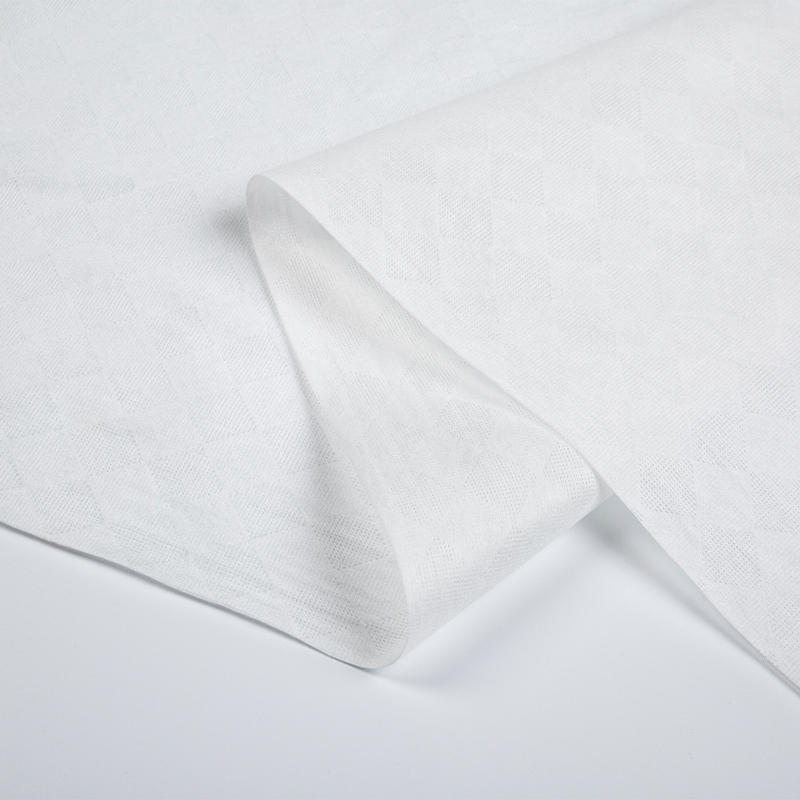