Founded in 2022, Hangzhou Shunlong Nonwovens Technology Co., Ltd. is a professional China nonwoven fabric manufacturer and non-woven raw material factory
1. Raw material selection and preparation
It is crucial to select high-quality fiber raw materials suitable for the spunlace process. Common fiber raw materials include cellulose fibers (such as cotton, linen, etc.), synthetic fibers (such as polyester, nylon, etc.) and regenerated fibers (such as animal protein regenerated fibers). These fiber raw materials need to have good spinnability and spunlace adaptability. In the preparation stage, fiber raw materials need to undergo pre-treatment such as cleaning, drying, and carding to remove impurities and improve the uniformity and dispersion of fibers.
2. Fiber mixing and glue opening
During the mixing and degumming process, fiber orientation and distribution are initially formed. Different types of fibers are mixed in certain proportions to meet the performance requirements of the product. The mixed fibers need to be degummed, that is, the fibers are mixed with water or other liquids to form a fiber suspension. In this step, controlling parameters such as the concentration, temperature and stirring speed of the fiber suspension helps to achieve uniform dispersion and preliminary orientation of the fibers.
3. Wet molding and fiber orientation control
Wet molding technology uses water as the dispersion medium for fibers, dispersing fiber raw materials in water to form a paper suspension, and then through a series of process steps, such as molding, dehydration, pressing, drying and post-processing, to finally form paper sheets or cardboard. In the production of spunlaced non-woven fabrics, wet forming technology provides a good environment for the uniform dispersion and orderly arrangement of fibers. Fiber orientation has an important influence on the properties of nonwoven fabrics. During the wet molding process, by controlling the orientation of the fibers, the fibers can be arranged in a specific direction, thereby improving the strength, softness and breathability of the non-woven fabric. At the same time, orderly fiber arrangement can also improve the appearance and feel of non-woven fabrics.
4. Spunlace reinforcement and fiber distribution optimization
Spunlace reinforcement is the core step in the production of spunlace non-woven fabrics. The high-pressure water flow impacts the fiber web to form entanglements and connections between fibers, thereby improving the strength and stability of the non-woven fabrics. During the spunlace process, controlling parameters such as water flow pressure, flow rate, injection angle and speed can optimize fiber distribution. For example, the use of high-pressure water jets can strengthen the entanglement between fibers and improve the density and strength of non-woven fabrics; the use of multi-angle and multi-level jetting can form a more uniform fiber distribution and improve the softness and breathability of non-woven fabrics. sex.
5. Post-processing and quality control
In the post-processing stage, through drying, calendering, winding and other processes, the spunlace non-woven fabric meets the final product requirements. At this stage, the fiber orientation and distribution are fine-tuned to further optimize product performance. For example, the orientation and distribution uniformity of fibers can be further improved through the calendering process; the thickness and width of non-woven fabrics and other dimensional parameters can be controlled through the winding process. At the same time, through strict quality control measures, such as sampling inspection, performance testing, etc., we ensure that the performance of non-woven fabrics meets standards and customer requirements.
When producing Spunlace Nonwoven Fabric, controlling fiber orientation and distribution is the key to ensuring superior product performance. By optimizing raw material selection and preparation, fiber mixing and glue opening, wet molding and fiber orientation control, spunlace reinforcement and fiber distribution optimization, as well as post-processing and quality control, uniform dispersion and orderly arrangement of fibers can be achieved to achieve softness. , breathable, high-strength, high-quality spunlace non-woven fabric with good stability.
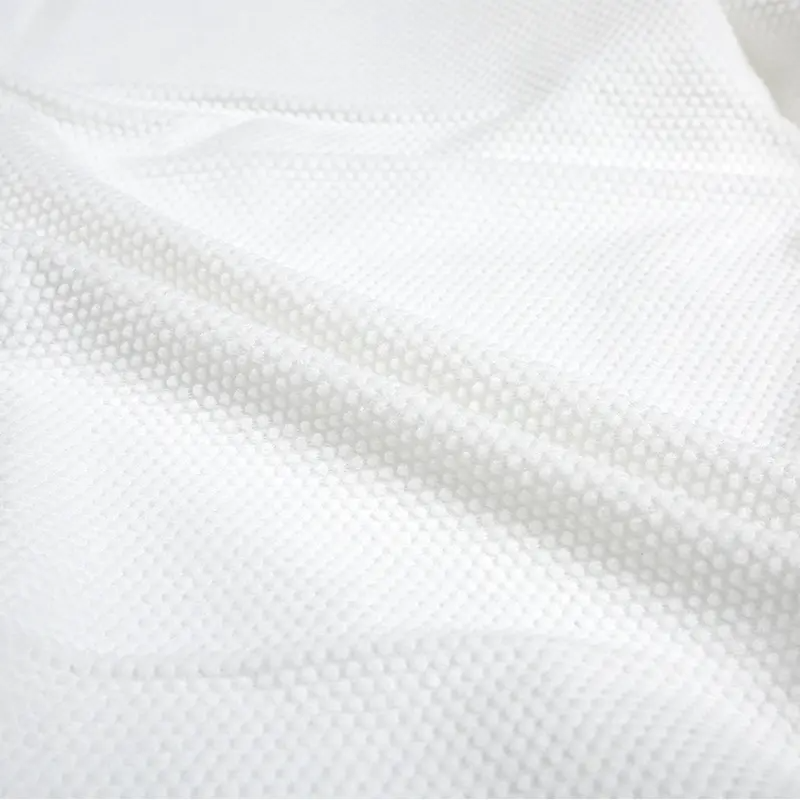